Choosing the right inventory method for your cannabis dispensary is not just a matter of improving efficiency; it’s critical for profitability, regulatory compliance, and operational fluidity. Cannabis dispensaries face a unique set of challenges due to the perishable nature of products and the highly regulated environment. This makes selecting the best inventory method one of the most important decisions for dispensary managers.
Inventory management systems directly impact every aspect of operations, from customer satisfaction to financial reporting and compliance with state laws. The right system ensures you can maintain the balance between having enough stock to meet demand and avoiding overstocking, which can lead to losses due to expiration or regulatory penalties.
Key Takeaways
- Effective inventory methods enhance efficiency and profitability.
- Cannabis dispensaries face unique inventory management challenges and regulatory demands.
- Choose an inventory solution tailored to your dispensary’s specific needs.
Cannabis Industry Specifics
Understanding the specifics of the cannabis industry is crucial for successful inventory management. Monitoring seed-to-sale tracking and managing a diverse product range are two critical aspects.
Seed-to-Sale Tracking Requirements
Managing a cannabis inventory involves much more than just keeping track of stock levels. Dispensaries must comply with seed-to-sale tracking requirements, which monitor every stage of the product lifecycle from cultivation to sale. Non-compliance can result in severe penalties, audits, and even shutdowns. Seed-to-sale systems integrate with state databases to ensure transparency. To avoid compliance failures, invest in robust tracking systems that minimize human error, such as automated barcode scanning or Radio Frequency Identification (RFID).
Managing a Diverse Product Range
Cannabis dispensaries typically offer a wide array of products—from flowers and edibles to concentrates, tinctures, and topicals. Each of these products has specific storage and handling needs. For instance, concentrates and flowers must be stored at precise humidity and temperature levels, while edibles have shorter shelf lives and stricter expiration date management. Successfully managing this diversity requires more than a basic inventory system. Automated inventory solutions help categorize products, manage perishable items, and send alerts when stock levels run low or expiration dates approach.
Factors to Consider when Selecting an Inventory Method
Choosing the right inventory method for your dispensary is crucial to maintaining efficient operations, compliance with regulations, and accurate financial records. Below are essential factors you should consider to make an informed decision.
Point of Sale (POS) System
Your POS system is the backbone of your dispensary’s operations. In addition to capturing sales data in real-time, it should integrate seamlessly with your inventory management system. POS system integration provides detailed reports on sales trends and product popularity, helping dispensaries forecast demand accurately to prevent out-of-stocks and overstocks.
Inventory Tracking System
Choosing the right tracking system is critical, particularly when managing large inventories across multiple locations. Inadequate or incompatible inventory tracking systems can cause significant compliance risks and operational issues for cannabis businesses.
For instance, MJBizDaily has reported that some Colorado dispensaries struggled with the implementation of the state's mandated Marijuana Inventory Tracking Solution (MITS), leading to compliance problems. Dispensaries reported difficulties integrating the system with their existing software, which required additional resources like purchasing RFID tags and data entry staff. This caused delays in compliance reporting, leading to operational inefficiencies.
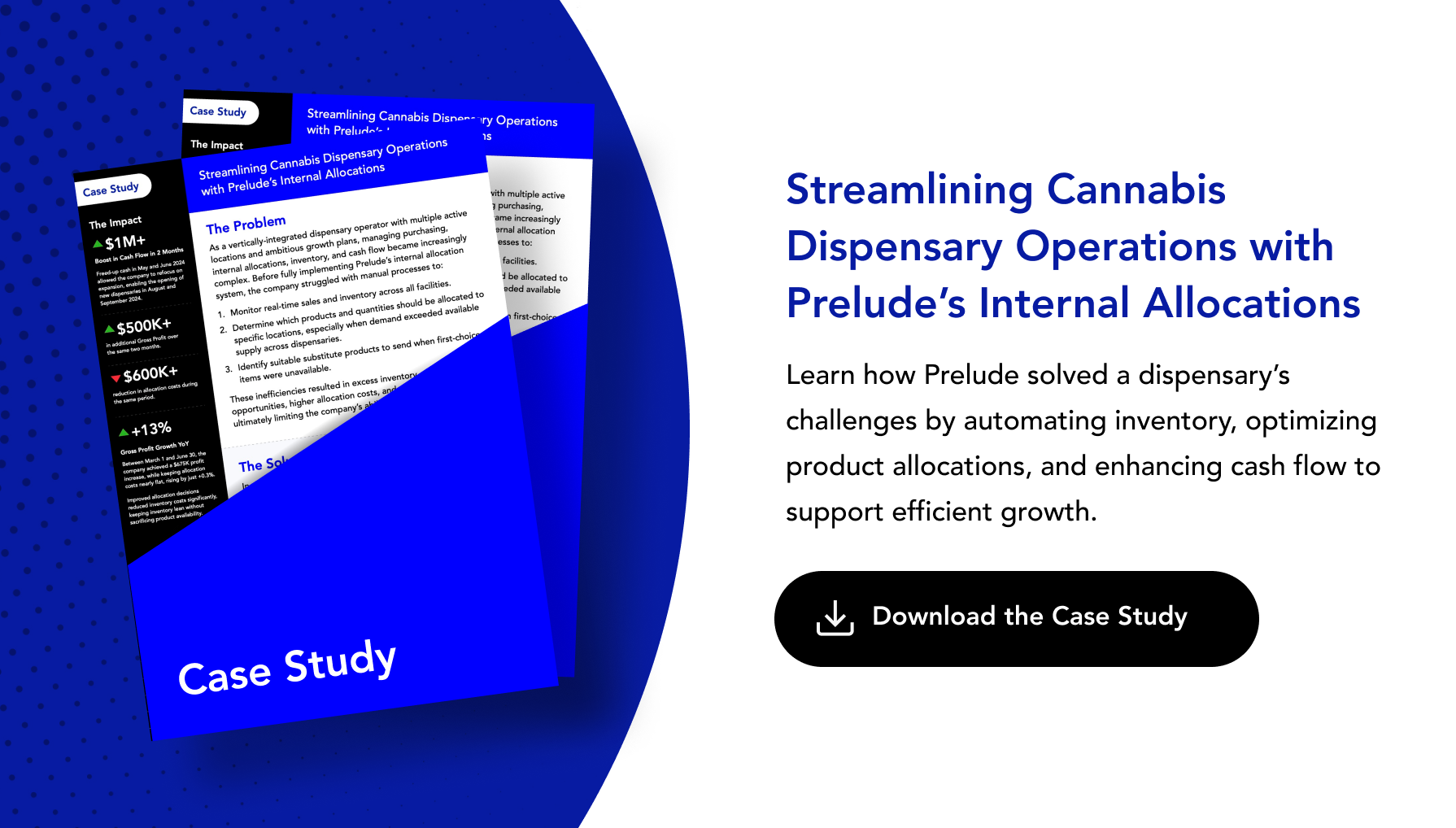
Compliance with State Regulations
Compliance with state regulations is non-negotiable for dispensaries. Different states have varying requirements for tracking and reporting inventory.
Factors to ensure compliance:
- Software compliance with state laws
- Automated reporting features to regulatory bodies
- Secure data storage and encryption
Choosing a compliant inventory method ensures you meet all legal obligations and avoid penalties or legal issues.
Different Inventory Methods for Dispensaries
Selecting the right inventory method is crucial for efficient operations and cost management in dispensaries. Each method offers unique advantages depending on your dispensary’s needs.
First-In, First-Out (FIFO) Method
The First-In, First-Out (FIFO) method prioritizes the oldest inventory items first. This is particularly useful for dispensaries to ensure that products with expiration dates, such as certain edibles or oils, are sold before they spoil. FIFO is straightforward and aligns well with day-to-day operations.
One significant benefit of FIFO is the accurate reflection of current market prices in accounting records. Your cost of goods sold (COGS) will be based on older, possibly cheaper, inventory, whereas your remaining inventory will be valued at more recent prices. This can make financial statements more favorable during periods of price inflation.
Weighted Average Cost Method
The Weighted Average Cost (WAC) method assigns an average cost to each unit of inventory. This is calculated by dividing the total cost of goods available for sale by the total number of units available for sale. It simplifies accounting and inventory management by averaging out price fluctuations over time.
For dispensaries, WAC can be particularly beneficial when dealing with a large and varied inventory. Unlike FIFO and LIFO, WAC smooths out the cost per unit, making it easier to manage complex inventories with varying purchase prices. This method helps maintain stable pricing for your products, enhancing predictability in your financial planning.
Last-In, First-Out (LIFO) Method
The Last-In, First-Out (LIFO) method prioritizes selling the most recently acquired inventory first. Though less commonly used in dispensaries, LIFO can be advantageous in certain tax environments. During periods of rising prices, LIFO can result in lower taxable income because the newer, and often more expensive, inventory is considered sold first.
One caveat is that LIFO may not be appropriate for dispensaries where products have perishability concerns. Also, it can result in older stock accumulating, which could lead to spoilage or obsolescence. As a dispensary owner, you need to evaluate whether the tax benefits outweigh the operational challenges.
Just-In-Time (JIT)
The Just-In-Time (JIT) inventory method focuses on minimizing inventory holding costs by ordering products only as they are needed for sales. This method can reduce excess inventory, waste, and storage costs, making it an attractive option for dispensaries looking to optimize cash flow.
However, JIT requires accurate demand forecasting and a reliable supply chain. Any disruptions in the supply chain can result in out-of-stocks, which can affect customer satisfaction. JIT is best suited for dispensaries with predictable sales volumes and strong supplier relationships.
Economic Order Quantity (EOQ)
The Economic Order Quantity (EOQ) method is a formula-based approach to determine the optimal order quantity that minimizes total inventory costs, including holding, ordering, and shortage costs. EOQ helps dispensaries balance the cost of holding inventory with the cost of ordering it.
This method is particularly useful for dispensaries with fluctuating demand, as it helps optimize stock levels without overstocking or understocking. While EOQ can reduce total inventory costs, it requires consistent monitoring and adjustments based on market trends and product demand.
Safety Stock
Safety stock is the practice of keeping a reserve of inventory to protect against unexpected demand spikes, supply chain disruptions, or delivery delays. For dispensaries, maintaining safety stock of popular products ensures that customers won’t face shortages, even during periods of increased demand.
While safety stock can reduce the risk of out-of-stocks, it also increases holding costs. Dispensaries need to carefully calculate safety stock levels based on sales history and lead times to avoid excessive overstocking, especially with perishable products.
Cycle Counting
Cycle counting is a method of inventory auditing that involves regularly counting a portion of the inventory, rather than doing a full inventory count at once. This method helps dispensaries maintain accurate inventory records and catch discrepancies before they become major issues.
Cycle counting can be done daily, weekly, or monthly, and is particularly beneficial for high-volume dispensaries that may struggle to do full physical counts frequently. Regular cycle counts can reduce the need for disruptive, large-scale inventory audits while maintaining accuracy.
Automatic Dispensing Machines (ADMs)
Automatic Dispensing Machines (ADMs) are automated systems that store and dispense products based on pre-set instructions. In a dispensary setting, ADMs can streamline the dispensing process, increase speed and accuracy, and reduce the risk of human error in inventory handling.
While ADMs can improve efficiency, their high initial costs and ongoing maintenance may be a barrier for smaller dispensaries. However, for high-volume locations, ADMs can significantly reduce labor costs and improve customer satisfaction by ensuring faster service and reducing wait times.
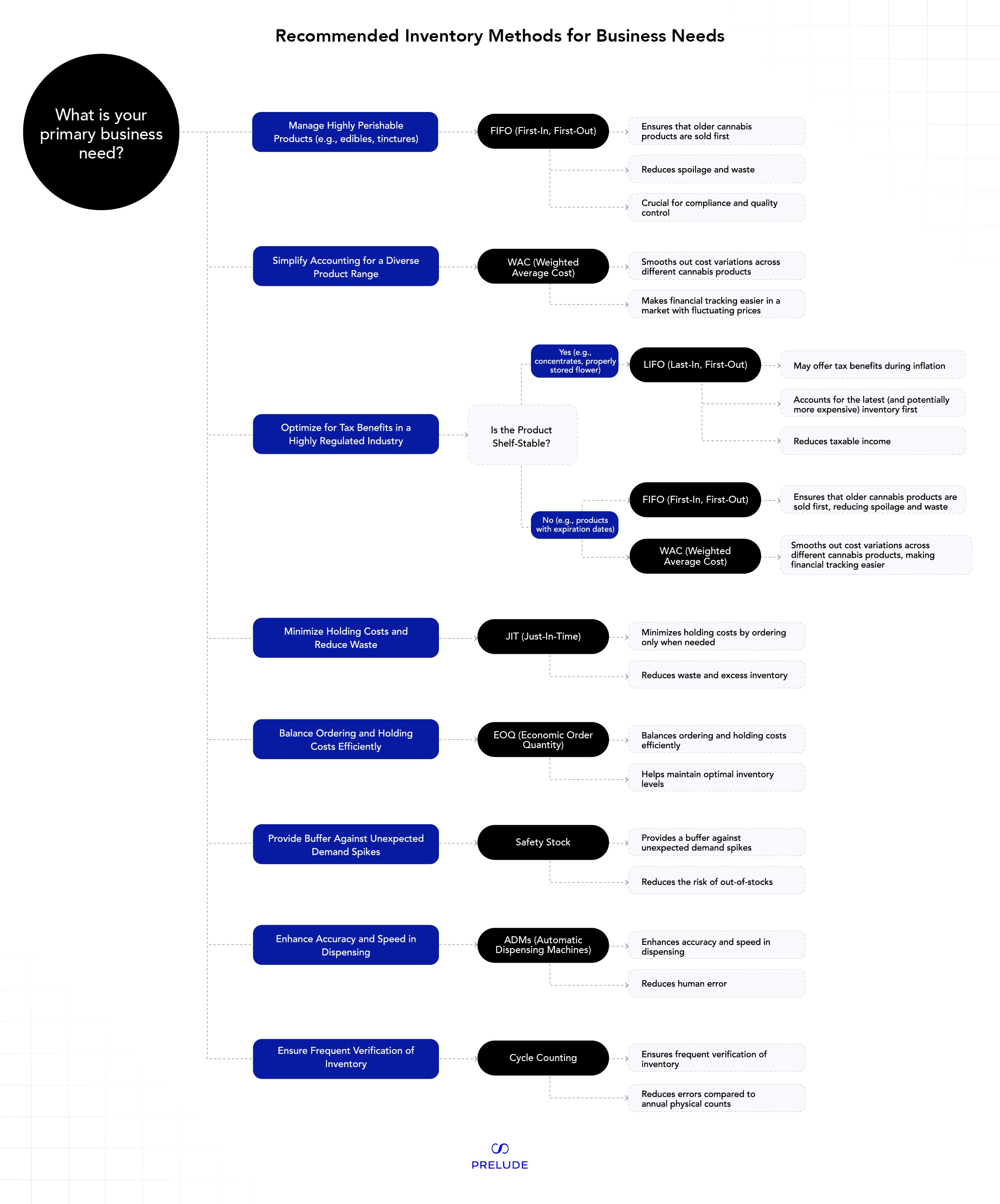
Implementing and Managing the Chosen Inventory Method
Manual tracking may seem cost-effective upfront, but it can lead to expensive mistakes over time. Prelude’s AI-powered system can help automate inventory methods used in cannabis dispensaries, reducing errors related to manual tracking. Here’s how Prelude could support each method:
- First-In, First-Out (FIFO): Prelude can automate stock tracking by setting rules to prioritize older inventory first, reducing spoilage and simplifying cost tracking.
- Weighted Average Cost (WAC) Method: Prelude automates the WAC method by tracking total costs and quantities of inventory purchases, calculating an average cost per unit. This simplifies accounting, smooths out price fluctuations, and is particularly beneficial for managing complex or varied inventories in dispensaries.
- Last-In, First-Out (LIFO): While LIFO is less common for dispensaries, Prelude’s inventory tracking can adapt to prioritize recent purchases.
- Just-In-Time (JIT): Prelude’s demand forecasting tools can automate replenishment, ensuring stock is ordered only when needed to minimize holding costs, and predict sales volume to prevent out-of-stocks.
- Economic Order Quantity (EOQ): Prelude can automate the calculation and tracking of EOQ by analyzing historical data and demand trends to balance ordering and holding costs.
- Safety Stock: Prelude sets up automatic alerts when stock falls below safety levels, ensuring that a buffer is maintained against demand spikes without overstocking and incurring excess holding costs.
- Cycle Counting: Prelude supports regular cycle counting by automating data collection and providing stock updates, reducing the need for disruptive physical counts while ensuring inventory accuracy.
- Automatic Dispensing Machines (ADMs): While Prelude doesn’t directly manage ADMs, it can integrate with them to ensure accurate inventory records, minimizing human error.
Simplify multi-location management, streamline compliance reporting, reduce out-of-stocks and overstocks, and improve your dispensary’s profit and cash flow with Prelude. Contact us today and get a free value discovery on how our software can optimize your inventory.