Vendor Managed Inventory or VMI and Consignment Inventory (CI) models are two distinct strategies designed to improve supply chain operations. Both approaches emphasize collaboration between vendors and buyers, aiming to optimize inventory levels, reduce costs, and create smoother workflows. Implementing VMI or CI can help businesses mitigate risks, enhance service levels, and build more resilient supply chains.
Vendor managed inventory vs consignment approaches offer unique operational benefits. VMI delegates inventory management to the vendor, who monitors stock levels and replenishes as necessary, allowing buyers to focus on core activities while benefiting from reduced holding costs and improved product availability. On the other hand, CI permits vendors to store their goods at the buyer's location, transferring ownership only when items are sold or consumed.
Both VMI and consignment inventory models offer unique advantages and challenges, with their suitability depending on factors such as the nature of the product, industry-specific dynamics, and the objectives of the supply chain partners. In certain scenarios, companies opt for a hybrid model, integrating elements of VMI and CI to maximize the benefits and address the challenges of both systems.
Key Takeaways
- VMI and CI offer distinct advantages in inventory management and supply chain collaboration.
- Choosing the right approach depends on organizational goals, product characteristics, and industry-specific factors.
- Hybrid models provide a balanced solution for more complex supply chains.
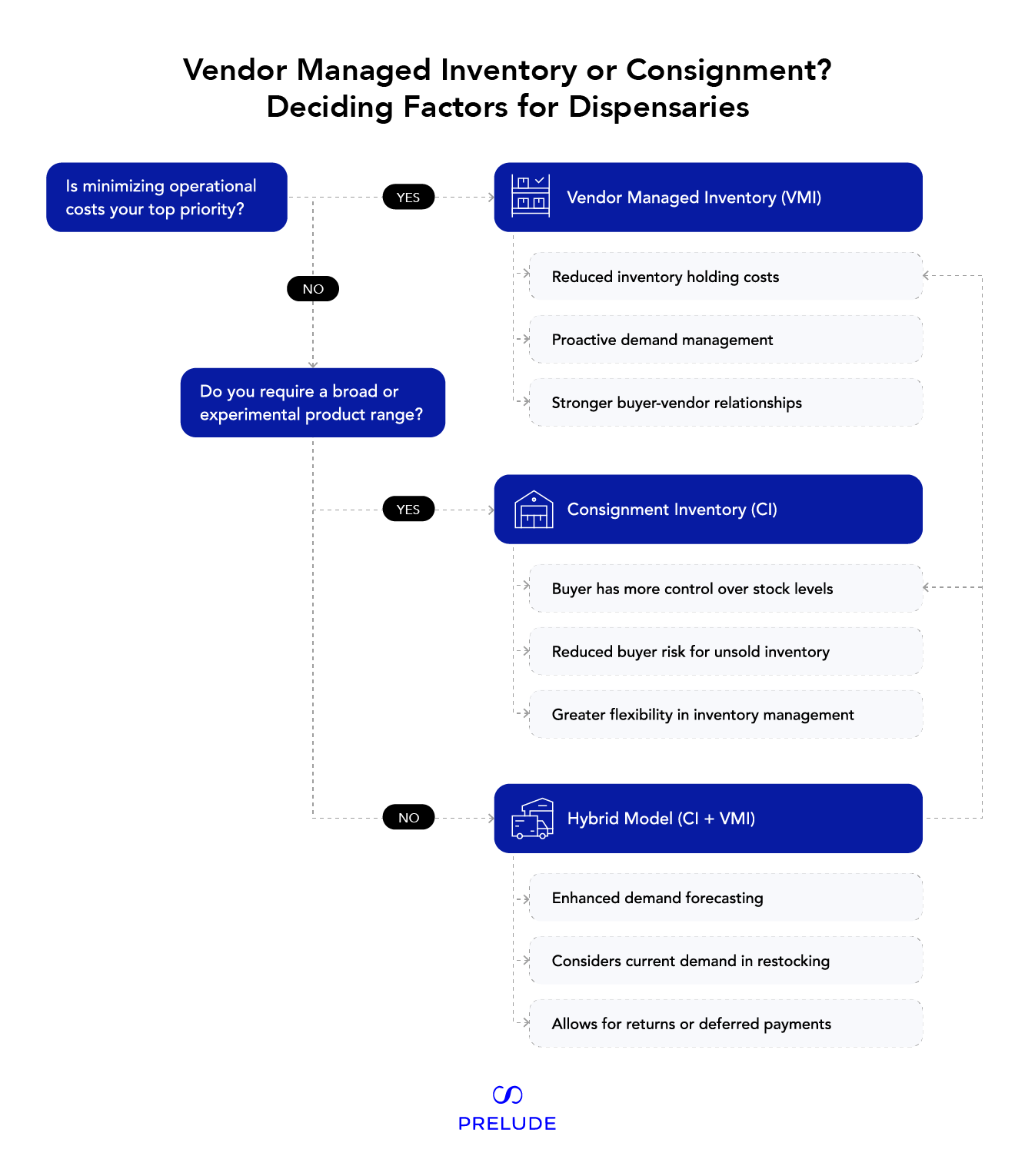
Vendor-Managed Inventory (VMI)
Vendor-managed inventory redefines the traditional buyer-supplier relationship by placing the responsibility for inventory management on the vendor. A collaborative VMI model ensures optimized inventory levels, faster replenishment, and better alignment of goals between both parties.
Definition and Mechanism
VMI operates on a simple yet effective principle: the vendor maintains the buyer’s inventory by regularly monitoring stock levels, forecasting demand, and planning replenishment cycles based on automated data. To enable this process, buyers often share inventory data through integrated systems such as Electronic Data Interchange (EDI) or cloud-based platforms.
Key components of VMI include:
- Inventory monitoring: Continuous tracking of stock levels and movements.
- Demand forecasting: Using historical data and market trends to predict future requirements.
- Replenishment automation: Triggering stock refills based on pre-defined thresholds.
- Performance tracking: Assessing outcomes using shared metrics.
Unlike traditional supply chains, VMI fosters a proactive partnership, where buyers must actively place orders. Vendors gain the autonomy to make inventory decisions, allowing them to align supply with demand seamlessly.
Benefits of VMI
VMI offers numerous benefits to both buyers and suppliers:
- Lower inventory costs: Vendors optimize stock levels, eliminating excess inventory and reducing storage expenses for buyers.
- Better cash flow: Buyers can allocate capital to other priorities instead of tying it up in inventory.
- Improved demand forecasting: Vendors gain insights into buying patterns, enabling more accurate production and logistics planning.
- Enhanced operational efficiency: Automation reduces manual intervention, streamlining procurement and replenishment processes.
Additionally, VMI encourages stronger relationships between buyers and vendors, characterized by better communication and shared insights. This partnership often translates into higher customer satisfaction, improved service levels, and greater long-term loyalty.
Challenges and Considerations
While VMI offers significant advantages, its implementation can be complex and challenging:
- Trust and transparency: Both parties must share accurate data and communicate openly.
- Technology requirements: Advanced IT systems are often needed for automated data sharing and inventory tracking.
- Role clarity: Clear delineation of responsibilities is essential to avoid disputes or inefficiencies.
- Risk sharing: Determining how to manage unsold inventory or demand fluctuations can be contentious.
Addressing these challenges requires careful planning:
- Establish clear service agreements: Define expectations, performance metrics, and roles.
- Invest in technology: Leverage inventory management software to ensure seamless integration.
- Regularly review processes: Conduct periodic assessments to refine operations and address emerging issues.
- Develop contingency plans: Prepare for unexpected demand shifts or supply chain disruptions.
VMI can become a cornerstone of a robust and collaborative supply chain strategy when executed effectively.
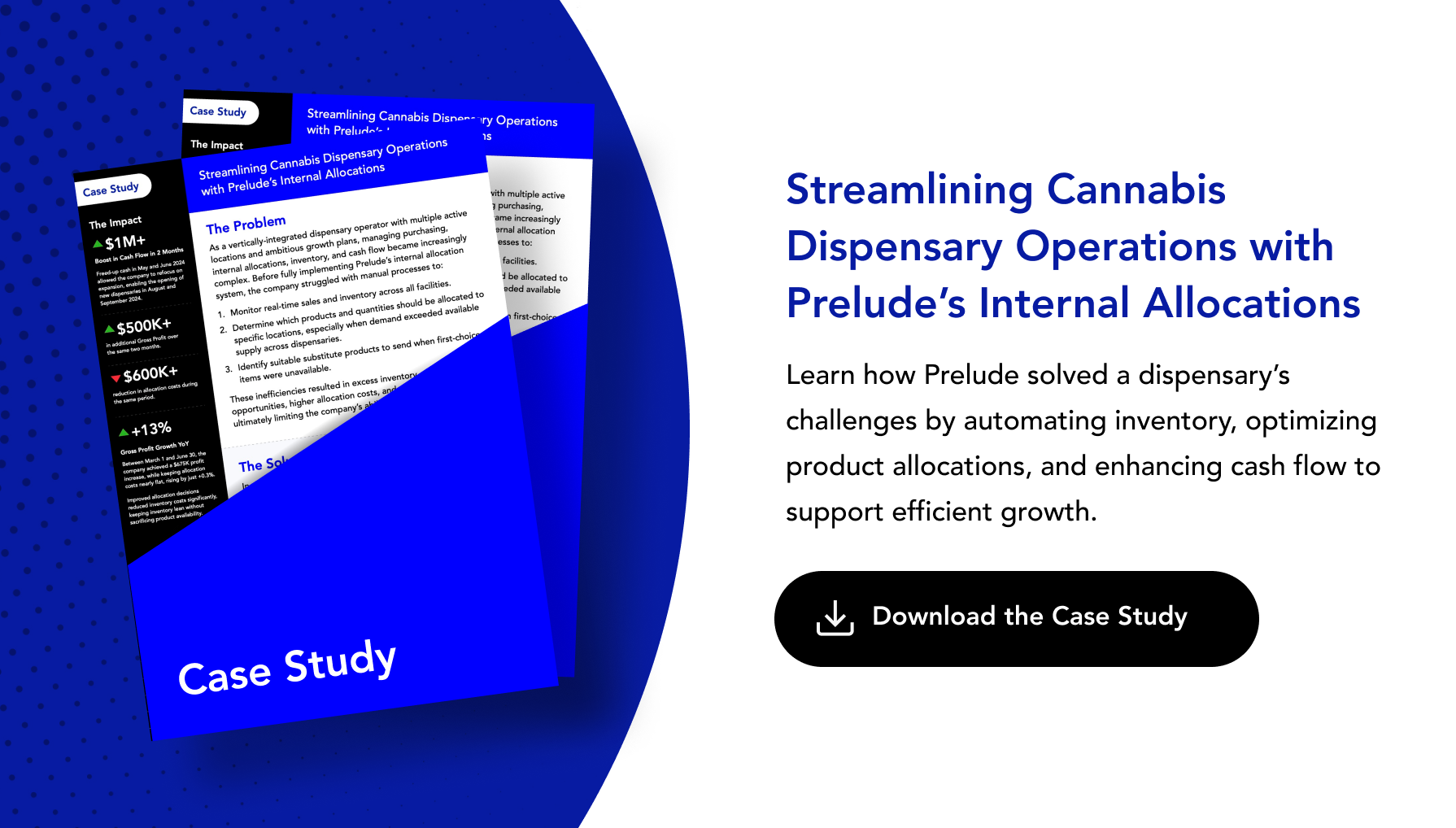
Consignment Inventory (CI)
Consignment Inventory offers an alternative inventory management approach by altering the traditional ownership dynamics between suppliers and buyers. The CI model enables buyers to reduce financial risk while ensuring they have stock readily available to meet demand.
Definition and Mechanism
Under the CI model, vendors retain ownership of goods until the buyer sells or consumes them. Products are stored at the buyer’s location; payment is made only after the items are used or sold. This setup shifts the financial burden of unsold inventory away from the buyer.
The vendor ships goods to the buyer’s warehouse or retail location. The buyer manages the day-to-day inventory handling, such as stocking shelves and tracking usage, but reports sales and usage figures to the vendor. Payments are typically made at regular intervals, such as weekly or monthly.
This model fosters collaboration by aligning vendor incentives with the buyer’s sales performance, ensuring both parties work toward maximizing product availability and minimizing waste.
Benefits of CI
CI provides several compelling benefits:
- Improved cash flow for buyers: By deferring payments, buyers can allocate financial resources to other business areas.
- Reduced risk of out-of-stocks: Vendors actively monitor and replenish inventory to maintain optimal stock levels.
- Better demand forecasting: Close collaboration facilitates accurate predictions of future needs.
- Shared risk: Vendors bear the cost of unsold inventory, reducing financial exposure for buyers.
For vendors, CI can boost sales by allowing buyers to stock a broader product range without the immediate financial commitment. Vendors also gain valuable insights into customer demand, enabling them to refine their strategies.
Challenges and Considerations
The CI model also introduces certain complexities:
- Operational intricacies: Accurate tracking systems and efficient communication channels are critical.
- Trust requirements: Strong partnerships are essential for seamless implementation.
- Inventory control: Buyers must carefully manage stock levels to avoid overstocking or understocking.
- Financial implications for vendors: Prolonged ownership of inventory can strain vendors’ cash flow.
Legal agreements play a pivotal role in CI arrangements. To avoid disputes, these contracts should address ownership, liability, payment terms, and inventory valuation. Furthermore, CI is best suited for non-perishable goods or items with stable demand, as products with short shelf lives or rapidly changing trends pose additional risks.
Comparative Analysis: VMI vs CI Supply Chain Comparison
VMI and consignment inventory models offer distinct advantages, but their impact on supply chain efficiency depends on the context. Analyzing the VMI vs CI effects on supply chain management and their operational and financial implications can help businesses choose the best fit.
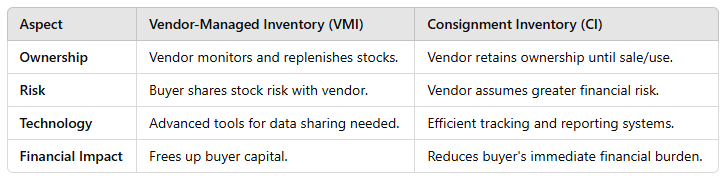
Operational Efficiencies
VMI promotes proactive inventory management, with vendors using automated data to optimize stock levels and minimize lead times, resulting in reduced out-of-stocks and smoother supply chain operations.
CI, while advantageous for buyers regarding risk reduction, may lead to challenges in aligning inventory with actual demand. Vendors might overstock buyer locations to ensure availability, potentially leading to inefficiencies.
Both strategies aim to balance inventory availability and cost control, but VMI’s data-driven approach often achieves greater operational precision.
Financial Impacts
VMI reduces buyers’ holding costs, freeing up working capital and improving cash flow. By deferring payment until goods are sold, CI offers buyers similar financial benefits while placing more risk on vendors.
The VMI vs CI effects on supply chain management are significant in this context, as VMI typically provides more predictable cash flow for suppliers, whereas CI can strain finances due to prolonged inventory ownership. These differences influence pricing strategies and cost-sharing arrangements.
Balancing Benefits and Responsibilities
While VMI fosters collaborative relationships through shared data and goals, CI reduces buyers’ financial exposure but increases vendors’ responsibility for inventory management. A hybrid approach blending VMI and CI often offers a balanced solution that maximizes benefits and minimizes risks.
Hybrid Model: CI&VMI
The hybrid CI&VMI model combines the strengths of both strategies, creating a flexible and collaborative inventory management system.
Definition and Mechanism
The hybrid model integrates consignment ownership with VMI’s proactive management. Vendors retain inventory ownership while overseeing replenishment based on automated data, ensuring optimal stock levels at buyer locations.
This setup includes:
- Vendor-owned inventory at customer sites
- Automated sales and usage data monitoring
- Automated replenishment decisions
- Jointly defined risk and reward mechanisms
A strong IT infrastructure and clear agreements are vital for this model’s success.
Benefits and Challenges
The CI&VMI model offers numerous benefits:
- Optimized inventory costs: Buyers and vendors benefit from reduced carrying costs.
- Increased responsiveness: Automated data enables faster demand adjustments.
- Shared risk management: Collaborative arrangements balance responsibilities.
However, challenges include:
- Implementation complexity: Requires advanced systems and high trust.
- Potential conflicts: Clear roles are essential to avoid disputes.
- Infrastructure investment: Robust systems are necessary for seamless operation.
Successfully implementing this model requires thorough planning, trust-building, and well-designed contracts.
Vendor Managed Inventory vs Consignment: Selecting the Best Model for Your Supply Chain
The right inventory model depends on a business’s unique needs, industry dynamics, and emerging trends. Choosing between VMI and consignment inventory models requires evaluating factors such as product characteristics and vendor relationships to ensure the optimal approach for long-term success.
Choosing the Right Model
Key considerations include:
- Product traits: VMI suits fast-moving goods, while CI fits slower-moving, high-value items.
- Relationships: Trust and data sharing are critical for VMI success.
- Capabilities: Vendors need forecasting expertise for VMI, while CI reduces buyers’ financial burdens.
Hybrid models can offer balanced solutions, combining the best of both approaches.
Future Trends and Considerations
Technological advancements are reshaping inventory management. AI and machine learning enhance forecasting, blockchain improves transparency, and IoT enables automated tracking. These tools help companies adapt to omnichannel demands and prioritize sustainability.
Businesses should explore:
- Cloud-based systems for inventory management
- Collaborative platforms for supply chain coordination
- Circular economy practices to reduce waste
Staying ahead of these trends ensures robust, future-proof inventory strategies.
When deciding between vendor managed inventory vs consignment, it's crucial to consider how each model aligns with your business goals. Understanding the VMI vs CI effects on supply chain management can help you choose the right approach to reduce costs, improve efficiency, and strengthen vendor relationships. Take the time to evaluate your unique needs and find the model that drives long-term success for your supply chain.
Revolutionize Your Inventory Strategy with Prelude
Simplify inventory management and boost efficiency with Prelude’s smart solutions. Prelude utilizes VMI to give you automated and powerful tools to reduce costs and stay ahead.
With insights from our VMI vs CI supply chain comparison, you can make the right inventory decisions for your business. Contact us today to optimize your inventory strategy and streamline your supply chain.